Water-Based Defoamers
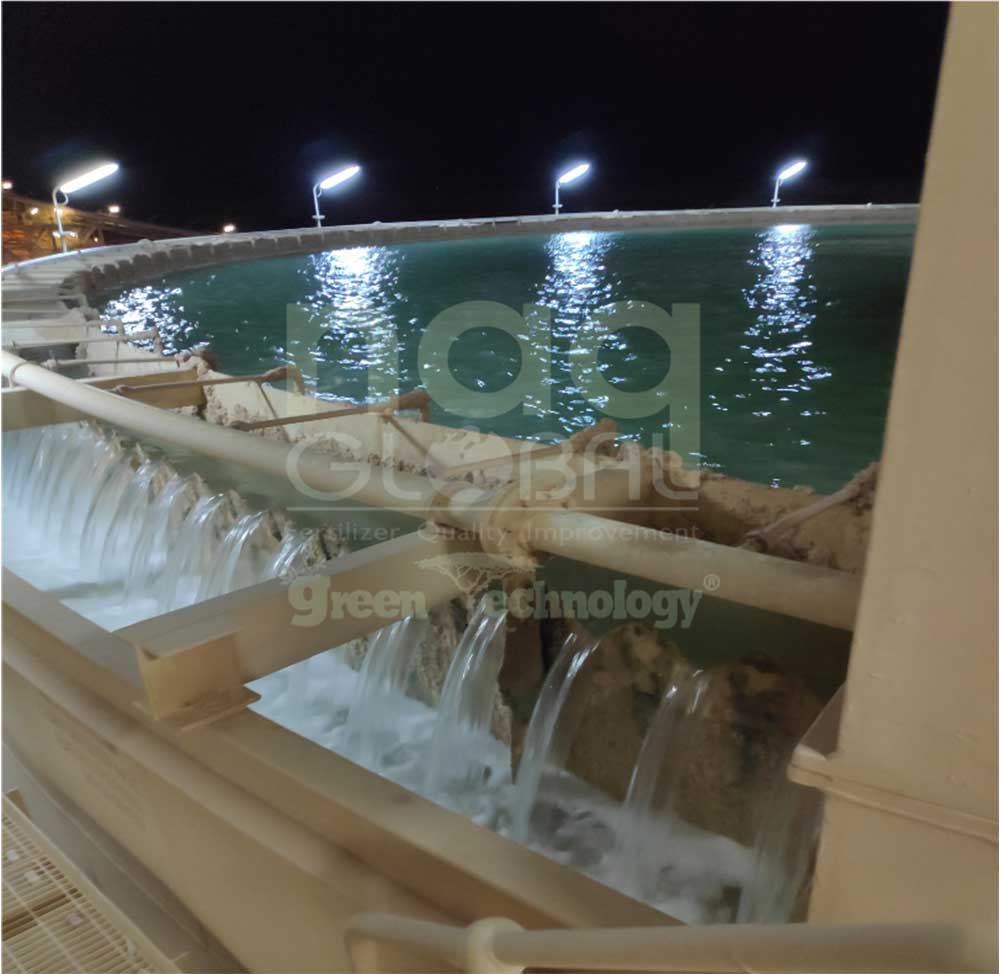
Flocculants And Filtration Aids
Green Technology-Based High-Performance Solutions For Effective Coagulation And Faster Filtration
Read MoreWater-Based Defoamers
If simply bifurcated, the word defoamer is composed of “de” and “foamer”, which implies those additives that help prevent the formation of foam or those additives that, when added to the already formed foam, pacify it, decreasing it wastage of the material. In industrial processes, while some foam generation might be benign, in phosphoric acid production, foam can pose serious problems.
Before we delve deeper into the concept of defoamers and how it is applied to phosphoric acid production, let’s discuss a little bit about the phosphoric acid production process.
Phosphoric acid is most economically produced through a now decades-old process involving reacting rock phosphate (typically coming from mines and undergoing a beneficiation process) with sulfuric acid or a mixture of sulfuric acid and varying strengths to give calcium sulfate and phosphoric acid. In this way, defoamers for phosphoric acid production are most commonly called producing phosphoric acid defoamer through the wet process.
There are typically many answers to this question, primarily because a lot of the foam depends on the kind of phosphate rock used in the reaction. After the phosphate rock is obtained from the mines, it often needs beneficiation to prepare the defoamer for phosphoric acid production. Several chemicals and solutions are used in the beneficiation process, and to get the optimum performance from a phosphate rock beneficiation process, NAQ Global’s mining products are excellent. A reason for foam generation is the characteristics of the flotation agents used as collectors for phosphate rock concentration. Thus, high-quality flotation agents, such as vegetable oil-based collectors made by NAQ Global, can optimize the process. Even after beneficiation, certain impurities in the phosphate rock can give several side reactions. Since phosphoric acid defoamer chemical is produced in large reactors, the problems from these side reactions are exacerbated. Foam generation is one of the biggest issues because of these side reactions, and foaming is further intensified depending on the rock and ore quality.
A lot of this foam amasses on the top of the reactor volume and is often difficult to be broken by mechanical means. Since this foam accrues on the top, the more the foam, the less the volume available for the reaction to occur in the reactor. Thus, foam generation drastically reduces the production capacity of the reactor and hence the production capabilities of the phosphoric acid plant. Thus, control of foam that accumulates on the top of the reactor is often a significant factor that determines the comfortability of operations of a phosphoric acid plant. Regardless of the phosphoric acid plant being DH, HDH, HH, Central Prayon Process, Di-hydrate Attack, and Hemi-Hydrate Filtration, foaming is the most common capacity limiting issue in the reactor. NAQ Global has developed a wide range of products for addressing all foaming issues in all types of phosphoric acid plants. Highly effective defoamers break the foam by acting on the surface tension to break bubbles created in the phosphoric acid reactor. Like the ones made by NAQ Global, sophisticated defoamers do not attack the rubber lining of the reactors.
NAQ GLOBAL manufactures and supplies specialty defoamer chemicals for Phosphatic fertilizer plants. Whether it is Hemihydrate, dihydrate, Hemi Di, or Di Hemi process, NAQ GLOBAL provides tailor-made defoamers – GREEN DEFOAM series for Phosphoric acid defoamer plants to give the best techno-commercial solution. We are the leading defoamer suppliers and manufacturers to the phosphate industry globally.
Traditional defoamers are typically oil-based defoamers. The utilization of conventional defoamers often presents a notable drawback: their tendency to corrode the rubber linings within reaction vessels. This issue, exacerbated by the oil-based composition of traditional defoamers, poses significant operational challenges in phosphoric acid plants. However, our pioneering water-based defoamers offer a transformative solution. Engineered with advanced formulations, these sophisticated agents are meticulously crafted to safeguard the structural integrity of reactor linings. By sidestepping the detrimental effects inherent in oil-based alternatives, our innovative products not only ensure seamless operations but also mitigate risks to critical infrastructure. Our most sophisticated water-based defoamers do not attack the rubber lining of the reactors. With these defoamers being completely water-soluble, fewer contaminants are handled in the ETP.
Defoamers play a crucial role in water treatment processes by controlling foam formation. Foam can hinder the efficiency of various water treatment operations such as filtration, sedimentation, and chemical treatment. Here are some key applications of defoamers in water treatment:
In phosphate rock mining, foam can accumulate due to the presence of organic matter, surfactants, or other contaminants. Defoamers are added to control foam formation during the treatment process, allowing for effective separation of solids and liquids. Different degree and quality of foams are required to separate particular minerals. The extraction of specific minerals during the mining process necessitates meticulous control over the generation and management of foams. The quality and purity of the extracted minerals are inherently intertwined with the precision with which foams are generated and regulated. Thus, the efficacy of mineral extraction hinges upon the adept management of foam dynamics.
NAQ Global provides excellent range of chemicals that can control foams. Within the realm of foam control solutions crucial to the mining industry, NAQ Global distinguishes itself through its commitment to sustainability and innovation. NAQ Global, a pioneer in the field, specializes in producing premium-grade foam control agents derived exclusively from vegan and vegetable sources, offering a comprehensive range of natural defoaming agents.
Embracing the ethos of eco-consciousness, NAQ Global harnesses the power of natural ingredients to develop highly effective foam control products tailored specifically for mining operations. These innovative solutions not only excel in performance but also uphold stringent environmental standards, aligning seamlessly with the evolving sustainability goals of modern businesses. By opting for vegan and vegetable-origin products, mining enterprises not only enhance the purity and quality of their extracted minerals but also achieve significant cost efficiencies over conventional alternatives.
Through its unwavering dedication to sustainability, coupled with a steadfast commitment to excellence, NAQ Global continues to revolutionize defoaming agents in the entire phosphoric acid supply chain, empowering businesses to achieve optimal operational outcomes while safeguarding the planet for future generations.